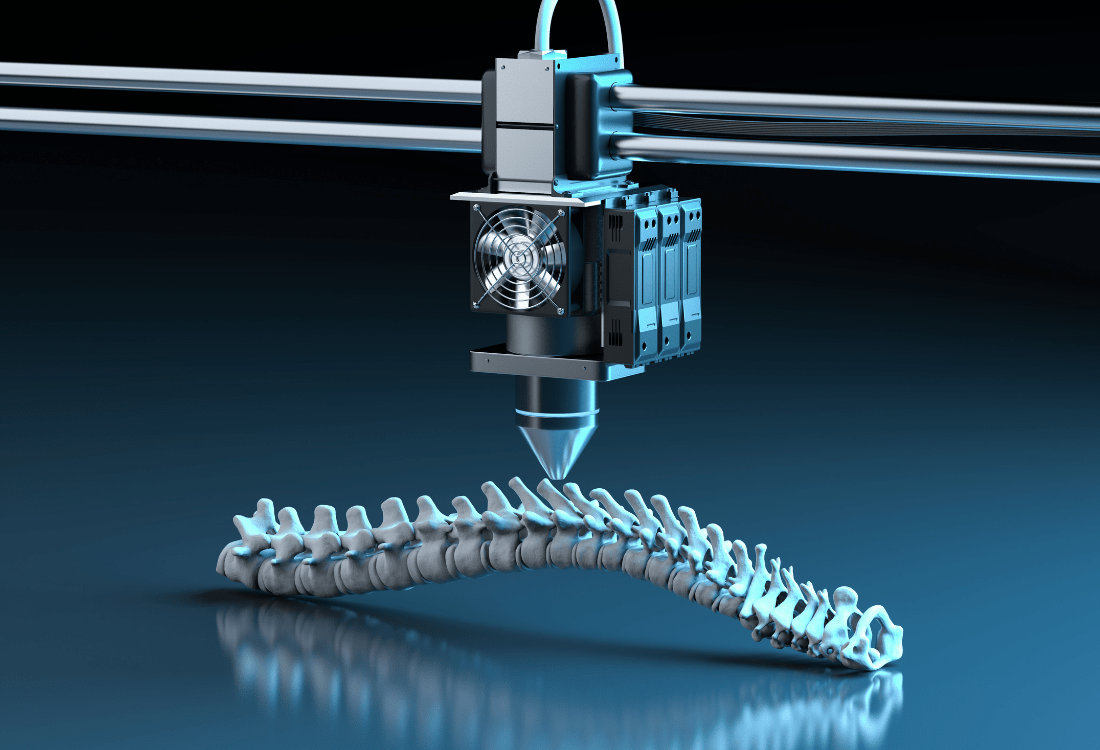
How Additive Manufacturing Is Revolutionising The Medical Field
Prototyping has been a staple of medical science for hundreds of years and is as relevant today as it was in 1816 when René Laennec created the world’s first medical device prototype, the stethoscope. While his invention - a simple wooden tube that allowed doctors to amplify heart and lung sounds – lags behind modern fabrication techniques and material processes, it laid the foundations for modern auscultation and advanced the design of medical devices.
For medical device manufacturers in the UK and across the globe, additive technology is revolutionising how products are designed, tested, and produced. In this article, we’ll explain why.
Delivering A Personalised Patient Experience
Additive manufacturing enables the creation of customised medical devices and tools tailored to the unique anatomical needs of each patient. Unlike traditional manufacturing, which relies on mass production to suppress costs and turnaround times, 3D printing techniques, allow for bespoke designs that enhance patient outcomes. Surgical instruments, in particular, can now be designed to perfectly suit each individual patient, overcoming a longstanding problem in medicine: how to deliver personalised care that reflects the individual idiosyncrasies of each patient while staying within budget.
Advancing Medical Research
In medical research, additive manufacturing has proven invaluable. With each medical condition manifesting in distinct ways, researchers can now produce precise anatomical models, such as replicas of cancerous tumours, offering new insights into how diseases develop and spread. Bespoke models enable scientists to study complex medical conditions and test drugs and treatment methods in a controlled environment, without exposing patients to unnecessary risk. By bridging the gap between theory and application, additive manufacturing in medical research accelerates the discovery of innovative cures and therapies.
Enhancing Speed And Adaptability
The timeliness and adaptability of additive manufacturing are other critical advantages for the medical field. The speed at which prototypes can be developed allows medical teams to respond rapidly to urgent needs: during the COVID-19 pandemic, for example, 3D-printed ventilator components were produced in record time to help Intensive Care Units provide complex care for soaring numbers of patients. Also, the compatibility of additive technology with biocompatible materials expands the breadth of applications for which it can be used, from bone scaffolds to tissue engineering. These advances demonstrate why additive manufacturing is increasingly necessary in the design and testing of medical devices.
Improving Precision And Production Efficiency
Production processes have also been revolutionised by additive manufacturing for medical devices. By utilising data from build programme optimisation, manufacturers can produce highly precise and reliable prototypes, streamlining the iterative design process and ensuring that final products meet rigorous standards. The ability to create multiple versions of a product with exceptional accuracy reduces time-to-market and enhances the overall quality of finished tools and devices.
Find Out More
At Complete Fabrication, we are experts in high-precision prototyping for the medical industry. Our ISO 9001:2015-compliant services include prototype assembly, delivering innovative solutions for complex medical applications that achieve exceptional accuracy, and giving specialists and patients confidence that procedures will be completed correctly and safely.
To find out more, or request a free no-obligation quotation for your next medical project, please get in touch today.
Image Source: Canva