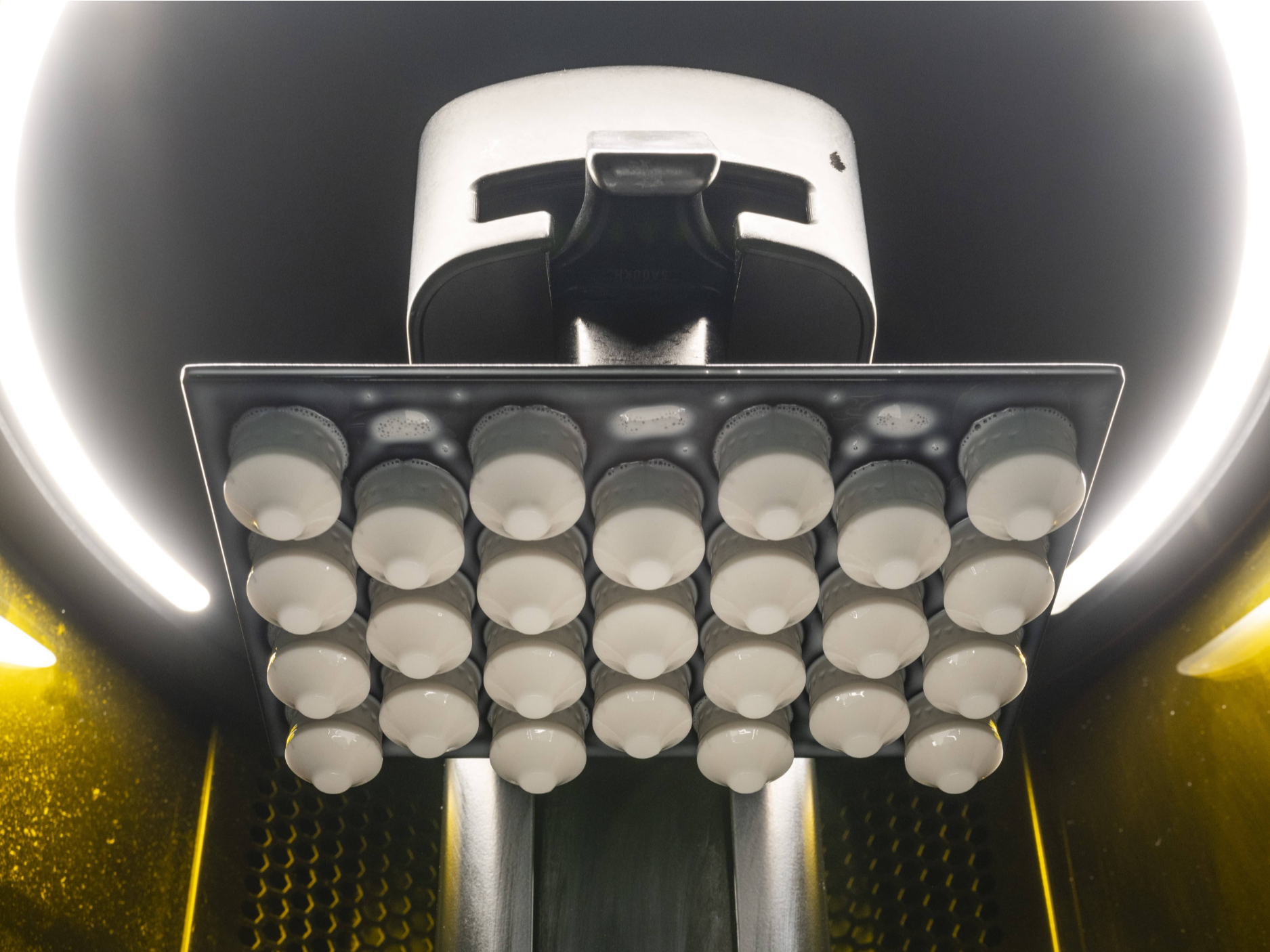
Vacuum Casting Vs 3D Printing: Which One Should I Choose?
3D printed parts have become popular in prototype manufacturing due to the method’s speed, cost-efficiency, and ability to create complex, intricate designs. Compared to vacuum casting, 3D printing is a relatively new technology, so designers may be reluctant to dispense with the tried-and-trusted methods of the past.
In fact, both 3D printing and vacuum casting excel in different ways, so it is important to appreciate their strengths and applications to make an informed decision. In this article, we’ll explore how these two techniques compare in terms of materials, time, cost, and finished product quality.
Materials
The choice of manufacturing method often depends on the materials used or the characteristics you would like to achieve. For 3D printed prototypes, plastic, stainless steel, titanium, resin, and nylon are commonly used due to their versatility and suitability for capturing CAD designs and intents. In contrast, vacuum casting uses materials such as epoxy, polyurethane resins, and silicones, which are ideal for replicating injection-moulded assemblies and creating durable, self-coloured parts with a flawless finish.
Time
If time is a critical factor, 3D printing is usually the option that delivers the quickest results. Unlike vacuum casting, it does not require moulds, enabling the quick production of prototypes. This flexibility makes 3D printing ideal for many iterative design processes. Vacuum casting, on the other hand, involves the manufacture of moulds, which can extend production times. However, although more time-intensive, vacuum casting is highly efficient for low-to-medium volume runs once the mould is prepared leading to consistent high visual quality results.
Cost
3D printing is known for its cost-efficiency in low-volume prototypes and productions. Its affordability stems from the absence of mould-making costs, the ability to produce single parts without complex tooling and the lack of labour content. The cost of vacuum casting depends on the complexity of the mould and the level of detail required in the final product. Highly detailed components tend to increase production expenses, making this method more suitable for projects where flawless aesthetics and durability are non-negotiable.
Finished Product
The complexity of your design can also influence your choice. 3D printing is unparalleled for intricate geometrical designs that may be challenging to achieve with traditional methods. However, despite its flexibility, achieving a flawless finish with 3D printing may require additional post-processing, which can increase costs and make the prototype less resilient. Especially for quantities above 3 parts or 3 assembles. In contrast, vacuum casting is renowned for delivering aesthetically refined, injection-moulded-like results. Final parts are often flawless, self-coloured, and ready for use in functional testing or as end-use components. This makes vacuum casting a preferred choice for projects that require “look like” finishes and durable finished products.
Meeting The Needs Of Each Project
Ultimately, the choice between vacuum casting vs. 3D printing depends on your project’s requirements. If speed, cost-efficiency, and complex designs are priorities, 3D printing is likely the better choice. For projects that demand superior aesthetics, fine details, or low-volume manufacturing of injection-moulded-quality parts, vacuum casting is a more suitable option.
For expert advice about which method is most suited to your next project, please get in touch with Complete Fabrication today.